Thursday, August 12, 2010
Adhesive Glossary
In case you’re not familiar with the adhesive terminology used in technical data sheets, websites and brochures, here’s a helpful jargon buster for the most common technical terms.
- Acrylic adhesives
- Two-component adhesives that have formulations that tolerate dirty and less prepared surfaces (generally linked to metals). They offer flexible bonds with good peel and impact resistance
- Adhesion
- The process by which two surfaces are held together by interfacial forces (surface attraction) or by mechanical interlocking
- Adhesive
- A substance which is capable of holding materials together in a useful fashion by means of surface attraction. Surface attraction results from placing a thin layer of adhesive between two objects
- Cohesive failure
- A failure mode where failure occurs within the body of the adhesive i.e. when adhesive is seen on both substrates in the same location
- Cure
- When an adhesive cures, it is converted from a liquid to a solid state. This may occur by cooling, loss of solvents or internal chemical reaction. Curing implies a type of physical or chemical change in the adhesive, while hardening or melting is reversible
- Fixture time
- The interval of time between the mixing of the two components and the time a bonded part can be removed from a mould without distortion
- Stiffness
- A materials ability to resist deformation when a load is applied
- Strain
- The elastic deformation caused from stress
- Stress
- The internal resistance to change in shape and size
- Structural adhesives
- Are capable of withstanding a ‘significant load’, the implication of this is that the adhesive must be able to withstand a great deal of stress
- Substrate
- A material which is held by an adhesive, it is a generic term for objects that are being bonded e.g. composite, metal or plastic
- Substrate failure
- A failure mode where the substrate fails itself before the adhesive bond
- Tension
- Is the stress resulting from pulling a material apart
- Toughness
- A measure of a materials ability to absorb energy
- Viscosity
- The resistance to flow or degree of thickening of a fluid
-
Working time The time between mixing the two components and when the adhesive becomes no longer useable i.e. skins over
Posted by Gurpreet Pawar, Marketing Executive, Rushden, UK
•
Advice | (3) Comments • Permalink
Tuesday, July 20, 2010
E-RA enter the finals of the Progressive Insurance Automotive XPRIZE
Having successfully passed all the tests (Acceleration/Braking, Lateral Acceleration Tests and the Avoidance Test), the E-RA has entered the final stage of the Progressive Insurance Automotive XPRIZE.
E-RA passed the technical inspection early on Monday morning as the first team. Next round of tests starting on Wednesday include efficiency runs such as urban and citycycle.
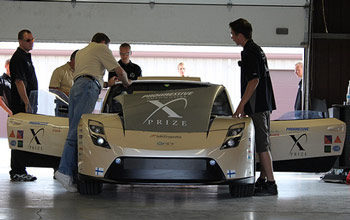
Posted by Gurpreet Pawar, Marketing Executive, Rushden, UK
•
Industry News | (0) Comments • Permalink
Friday, July 09, 2010
Adhesive Selection
Adhesives are now an important part of component design, they have come a long way since the early days and are now more than a match for most joining methods. They can actually improve component strength and durability, and save time and money in the process.
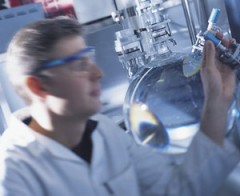
A good adhesive joint can be stronger than the material it is bonding, spread the load over the whole area, increase the durability of the whole assembly, and even reduce the cost per part.
Selecting an adhesive for a bonding application is best done during the design procedure when parameters can be outlined and determined. This makes the adhesive selection process easier. The user must first determine the process constraints and the conditions to which the final bonded assembly will be exposed. Then the substrate and adhesive selection can be made. Involving the adhesive manufacturer at this early stage can omit any later problems associated with wrong selection which can result in delayed production and field failures.
In addition, the main factors which need to be defined for the application before choosing the adhesive are:
- What are the substrates?
- What is the function of the bonded assembly?
- What stresses will the adhesive see (shear, peel etc.)?
- To what environmental/durability conditions will the final bonded assembly be exposed?
- What is the required bond line thickness?
- To what temperatures will the adhesive be subjected?
- What are the plant environments where the adhesive will be used?
- What are the working / fixture times required?
- How will you apply the chosen adhesive?
Once these factors have been determined, testing can be carried out at our European Testing Centre to ensure the correct adhesive is chosen for the application in question.
Posted by Gurpreet Pawar, Marketing Executive, Rushden, UK
•
Advice | (0) Comments • Permalink
Tuesday, June 29, 2010
Understanding Methacrylate Technology
Plexus adhesives are methacrylate adhesives that have been developed to perform under a wide range of conditions. This is achieved by improving curing, bonding, adhesion and toughening mechanisms.
The free radical cure mechanism of Plexus methacrylates is catalytic in nature. When the adhesive and activators are mixed, amines in the adhesive cause the peroxide to decompose into free radicals, which initiate the process of chain polymerisation of the MMA to PMMA. These reactions are exothermic and take place at room temperature removing the need for applying heat to initiate the cure.
The improved adhesion mechanism of methacrylate adhesives consists of the low viscosity monomer solvating the surface of most thermoplastics prior to the curing mechanism beginning. The monomer can solvate most surface contaminants which removes the need for any surface preparation prior to applying the adhesive.
Plexus methacrylate adhesives have a unique combination of polymers and impact modifiers which enable them to be strong yet flexible. The resulting high tensile strength along with impressive elongation (over 100% at @ 30o C) gives them the processing advantages and convenience of epoxies and polyurethanes
The total combination of all these factors along with good rheology, thixotropic properties, ease of use and lack of VOC’s and solvents, results in a range of structural methacrylate adhesives that can be successfully used in the marine, construction and automotive markets on a wide range of substrates.
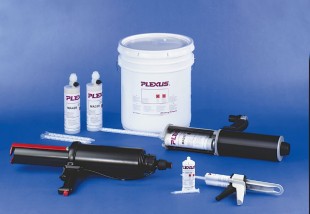
Posted by Gurpreet Pawar, Marketing Executive, Rushden, UK
•
Advice •
Product | (1) Comments • Permalink
Wednesday, June 23, 2010
ITW Plexus Structural Adhesives workshop at JCB
The second stop in the ITW Plexus workshop tour (UK) was at one of the world’s largest construction equipment manufacturer’s – JCB. The workshops started at the JCB Cab Systems site and then moved on to the JCB World Headquarters.
The workshops are designed to give employees from different departments the opportunity to learn and ask questions on the benefits of using Methacrylate structural adhesives and the impact they have on production and business, as well as discussing surface preparation and bonding in practice.
The workshop was managed by Chris Coll (Territory Manager – UK & Ireland) and assisted by myself. The adhesive workshop received an enthusiastic response from its visitors, with the bonded samples and the infra red camera housing once again proving to be of great interest.
Posted by Abarmettler, ,
•
Events | (0) Comments • Permalink
Friday, June 18, 2010
Using structural methacrylate adhesives in the bonding of thermoplastics and composite materials
The use of adhesives in industry has increased significantly in recent years, but with the development of methacrylate technology the advance of structural adhesives has seen improvements in manufacturing techniques in many markets. Their versatility and ease of use means that the continued evolution of processes and materials is not held up waiting for joining methods to catch up. Components can be made light weight and durable without compromising on the finish of the overall part.
The term ‘structural adhesive’ typically defines an adhesive which can withstand high loads under a variety of different stresses for long periods of time. Structural adhesives are typically high molecular weight molecules, which are required to withstand and distribute the loads within a joint.
The reasons for using adhesive in preference to a mechanical fastening are two fold. Mechanical fastenings can cause stress around the fixing, resulting in stress cracking and where possible failure of the substrate. Adhesives can remove this. The bond line between the two materials produces lower stresses because the load is applied over a larger surface area. Along with this the adhesive provides a layer between the materials that can absorb energy in impact, allow for thermal expansion and act as a layer to resist fatigue.
Plexus methacrylate adhesives offer an alternative to many traditional methods of joining two substrates together. They posses the high strength of an epoxy combined with the flexibility of a polyurethane, due to unique combination of polymers and impact modifiers. The free radical chain-polymerisation cure of methacrylate adhesives means they cure at room temperature and are not as susceptible to off-ratio mixing. Many thermoplastics, composites and metals can be bonded with Plexus adhesives with little or no surface preparation. The bonding of dissimilar materials can be achieved successfully which means more industries can benefit from using adhesive. The use of an adhesive over other methods can reduce labour costs and increase productivity as well as providing a strong, flexible, tough, durable bond that can withstand fatigue vibration and impact.
The combination of all these factors combined with good rheology, thixotropic properties, ease of use, recyclability, and lack of VOC’s and solvents, results in a wide range of structural methacrylate adhesives that can be used to bond many substrates in a variety of different industries.
Posted by Gurpreet Pawar, Marketing Executive, Rushden, UK
•
Advice | (1) Comments • Permalink
Friday, May 28, 2010
Charity Head Shave
Technical team member Gary Coldwell has been busy raising money for charity.
Crazy Hats Breast Cancer Appeal is a Northamptonshire charity that supports women and men who are going through treatment for breast cancer. They raise money for work at the two major hospitals in Northampton and Kettering and they work with the Breast Reconstruction Team at Leicester Royal Infirmary.
Gary took part in a charity head (and beard) shave on May 16th 2010 at Bugbrooke Rugby Club. So far Gary has raised over £400.
Posted by Abarmettler, ,
•
People | (1) Comments • Permalink
Monday, May 10, 2010
Top speed of 200 km/h, with acceleration of 0 – 100 km/h in 6 seconds. Impressed?
But what if I tell you it’s a battery driven sports car?
The Electric RaceAbout (ERA) is a project by Helsinki Metropolia University of Applied Sciences, which ITW Plexus has been supporting for the past couple of years.
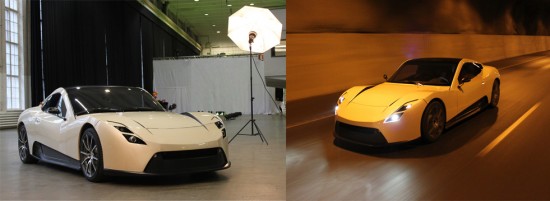
The challenge for the project team was to create the next generation battery driven sports car. The ERA has been designed to adopt the latest technology of electric powertrain to become a state of art battery driven electric-vehicle and manufactured using Carbon Fiber monocoque and features 4 electric drives (one motor per wheel).
A full-bloodied sports car with extremely low energy consumption and no emissions, will really open a new era for motoring enthusiasts.
The project team is now in the USA to participate in the Progressive Automotive X PRIZE, which will be awarded in October 2010. You can follow their progress via our blog.
Posted by Gurpreet Pawar, Marketing Executive, Rushden, UK
•
Industry News | (1) Comments • Permalink
Tuesday, April 27, 2010
ITW Plexus Structural Adhesives Workshop
ITW Plexus Structural Adhesives Workshop at Leyland Trucks.
The first Structural Adhesives Workshop of 2010 was held at Leyland Trucks on Friday 23rd April. The event was hailed a success by all who took part. The open forum format enabled people from all different departments to share ideas and ask questions on the use of adhesives. Chris Coll (Territory Manager - UK & Ireland) and Sally Sinai (Technical Support Manager) fielded the questions on the day while a wide variety of engineers tried to break the samples and figure out what the infra red camera housing, brought as a demonstration, actually was.
Posted by Abarmettler, ,
•
Events | (0) Comments • Permalink
Thursday, April 22, 2010
Structurally Green
A current factor that affects industry is the Environment and the impact that industry has on it. The word ‘green’ refers to the Environment and the efforts in reducing or eliminating harmful by-products, emissions and waste.
So, who measures ‘green’?
Obviously there are independent organizations such as Government agencies (e.g. HSE), industry groups like BASA and Greenguard Environment Institute (GEI). There are also the customers and the manufacturers.
A Methylmethacrylate (MMA) is a two component, structural adhesive. They provide an alternative for traditional assembly methods. In terms of ‘green’ MMAs offer several advantages:
• Low VOC emissions
• Less than 0.5% VOCs
• No Off-gassing issues
• Safe for indoor and closed locations
• Recyclability
MMAs eliminate toxins to the greatest extent possible. Products are developed with as much focus on human health as on the performance and this reduces the hazardous or toxic materials considerably. Unlike traditional assembly methods MMAs offer regrindability.
Posted by Abarmettler, ,
•
Product | (0) Comments • Permalink
Monday, April 19, 2010
JEC 2010 Review
JEC is one of the eagerly awaited exhibitions in the composites industry with hundreds of companies globally exhibiting. The exhibition did seem quieter than last year. This could be put that down to the effects of the recession or that many of the Resin manufacturers did not attend as they did in 2009.
Overall a good show, demonstrating different applications within the composite industry, some of which can be seen below.
On arrival we found ourselves being drawn to the Lamborghini. Italy was the honorary country so Lamborghini had the Tevatron on display.
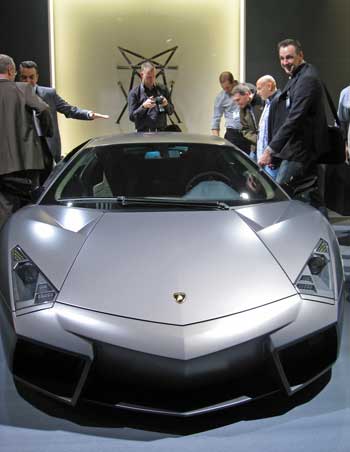
Lamborghini Tevatron
Having spent most of the day visiting the stands, we did come across some interesting applications using composites in particular the soccer shoes, manufactured using Tepex by Bond Laminates.
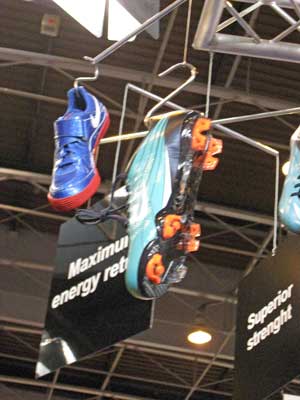
It’s raining shoes
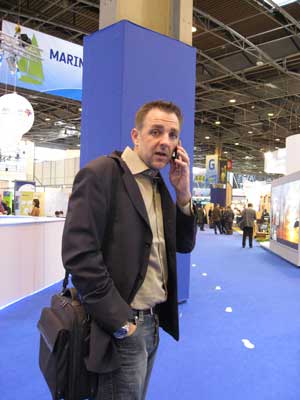
Jean-Charles ‘It’s a tough job, but someones gota do it’
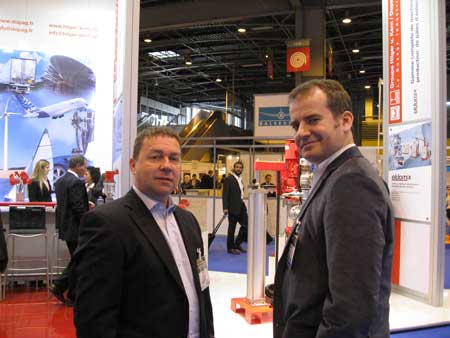
Mike Howard and Alex Grazia
As always, the Innovation showcase had on display some impressive applications, a few of them include;
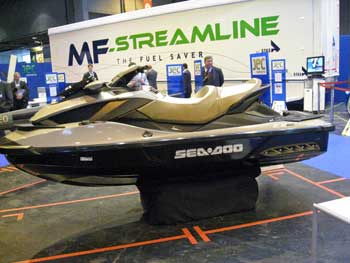
Motomare ski boat by Krauss Maffiei
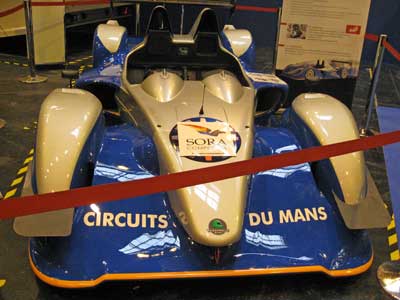
Composite Chassis Carbon Safety cell for a race car by Sora Composites
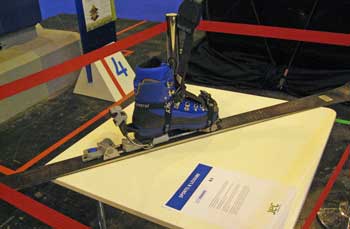
Mountain spring on a conventional mountaineering boot, a binding for turning and an ultra light carbon ski used by famous Skiers and Alpinist, by Alp Control
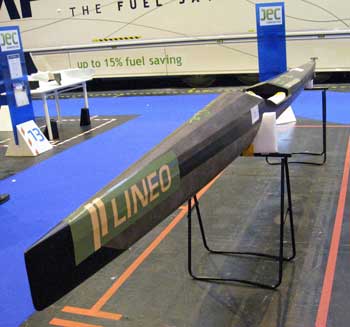
Composite Kayak by Kiln
It’s the one time of the year in which the majority of our distributors gather at one place. It was a pleasure to have met them all and reflected on what was happening in the marketplace and to discuss the show.
Although the volcanic ash is playing havoc with travel plans we hope you had a safe journey back.
ITW Plexus will be exhibiting at the JEC in 2011, so hope to see you then.
Posted by Gurpreet Pawar, Marketing Executive, Rushden, UK
•
Events •
Industry News | (0) Comments • Permalink
Thursday, April 01, 2010
2009 Plexus distributor of the year awarded to Ulbrich
During a recent visit by Kevin Lacey, Frank Senden and me to the Ulbrich facility in Austria we had great pleasure in awarding the distributor of the year award for 2009.
This is a new award that we felt would act as a sign of our thanks for the work and effort displayed by our distributors. We intend to make this an annual event and hope that all our distributors take up the challenge in order to be our next recipients. The criteria for winning this award included excellence in the sales process and value added initiatives.
2009 was a difficult year for everybody and some markets were affected more seriously than others. A number of projects that we were all expecting to start were pushed back and the reduction in outputs meant that we were all fighting to limit the negative figures. Ulbrich encountered these same issues and embarked on a strategy to solidify their approvals and position for projects that would start later and also diversify from its traditional markets and looking for new projects. They did this and were rewarded with some good projects last year and also a great start to 2010 with a number of the delayed projects picking up pace.
With this in mind it gave us great pleasure in presenting this award to them and we shared a few beers and a great meal to celebrate.
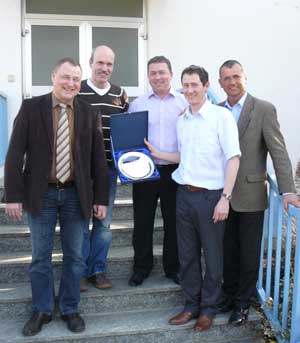
(Left to Right) Frank Senden, Jürgen Kaupp, Mike Howard, Iain Ford and Johannes Ulbrich
We look forward to being in a position to select our next winner at the end of 2010 and take this opportunity to thank all of our distributors for their fantastic efforts during 2009.
Once again congratulations to Ulbrich and let the competition for 2010 begin.
Posted by Mike Howard, European Business Manager, Rushden, UK
•
Company News | (0) Comments • Permalink
Monday, March 29, 2010
ISO 14001:2004 Certified
We’re doing our part to protect the planet.
Our European site based in Shannon, Ireland has recently been audited by BSI (British Standards Institution) and awarded the ISO 14001:2004 certification.
The certification is to ensure we take our responsibility towards protecting the environment seriously…which we do, and we are committed to reducing our environmental impact.
For further details visit http://www.itwppe.eu.
Posted by Gurpreet Pawar, Marketing Executive, Rushden, UK
•
Company News | (0) Comments • Permalink
Friday, March 26, 2010
JEC Composites Show 2010
It’s that time of the year… Porte de Versailles, Paris will again play host to possibly the largest composites show - JEC.
JEC is renowned for bringing all the major players within the composites and associated industries together under one roof. The Plexus team from both Europe and USA will be attending the show over the three day period. Although we will not be exhibiting, we will all be visiting and attending seminars, and very much look forward to meeting distributors and customers.
If you can’t make it, then follow us on our blog page, Facebook or Twitter.
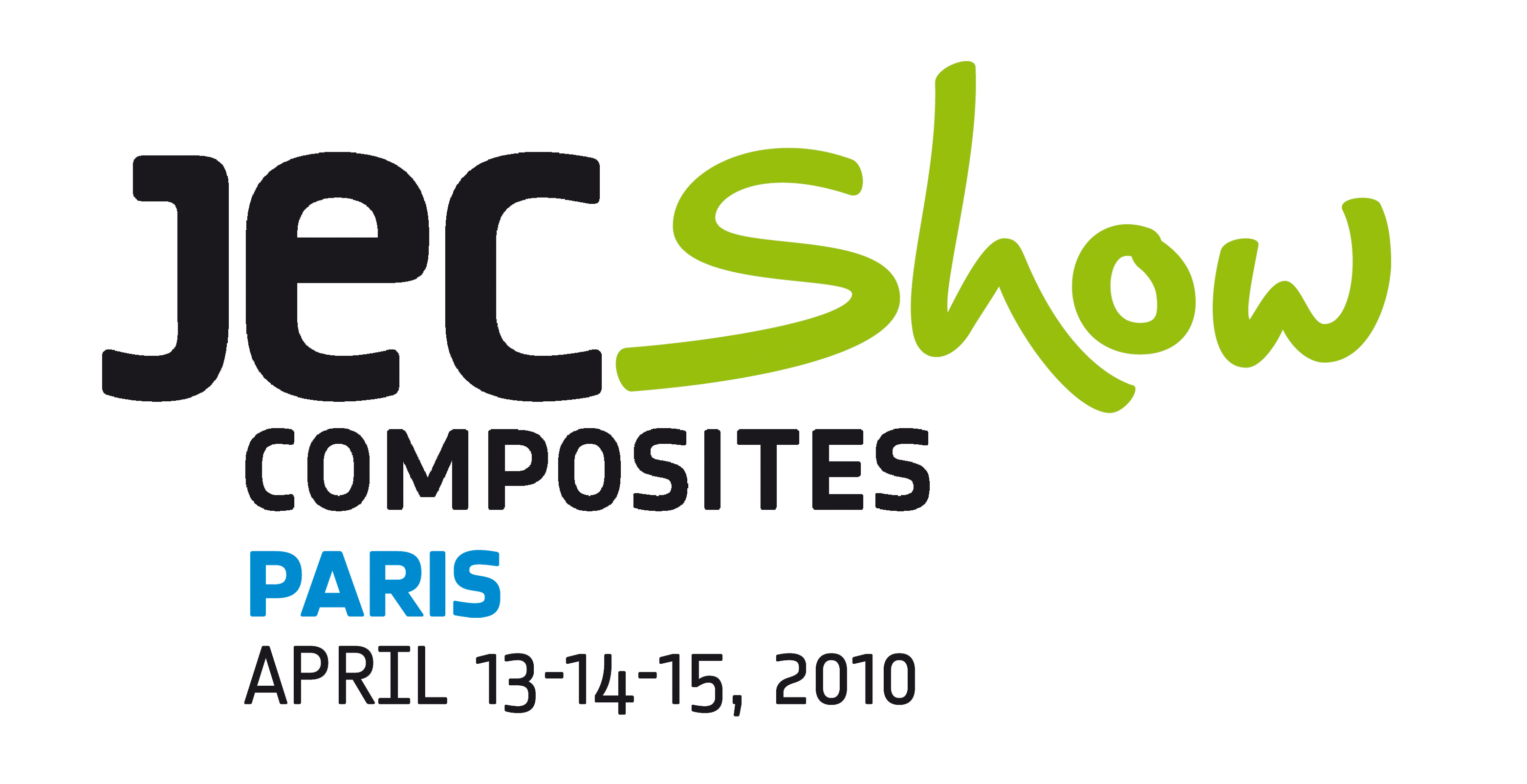
Posted by Gurpreet Pawar, Marketing Executive, Rushden, UK
•
Events | (0) Comments • Permalink
Thursday, March 18, 2010
NCS Resins Four Cities Tour
Once Kevin Lacey (Western Europe and ROW Manager) managed to arrive to a hot South Africa (30oC) we got started. Apparently the M25 was congested, causing him to miss his flight. The M25 (for those that do not know) is a UK motorway as Kevin tried explaining to us South Africans who travel on sand roads. 
The joint NCS Resins and ITW Plexus four cities tour kick started in Johannesburg last week at the 5-star Silver Start Casino.
The three hour workshop had a great reception with over 40 in attendance. The workshop began with a presentation from Kevin Lacey about himself and the business. Kevin then continued with my team discussing the benefits of Plexus structural adhesives, how they can improve manufacturing processes, reviewing and advising on application techniques as well as a practical demonstration giving customers the opportunity to bond different substrates.
The visitors enjoyed the opportunity to discuss the use of adhesives and existing customer’s found it helpful to know how they can further improve production techniques.
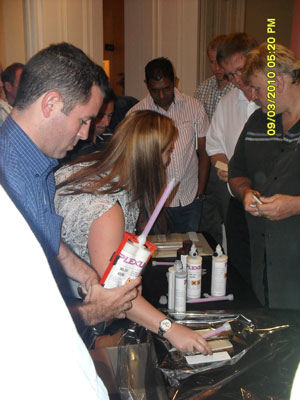
Plexus Demonstration: Ross Harris (NCS Sales Rep); Debby Burns and Customers
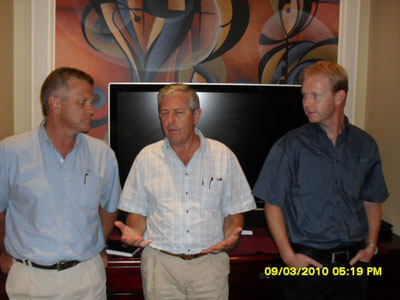
Paul Heunis (Johannesburg Branch Manager); Andre Immelman (MD); Shane Savage (Sales Rep)
The tour continued during the week to Cape Town, Port Elizabeth finishing in Durban on Monday 15th. Judging by the number of enquiries we have already received the tour was a great success.
Posted by Debby Burns, Accessories Product Manager, South Africa
•
Events •
People | (0) Comments • Permalink
Page 3 of 4 pages < 1
2 3 4 >